In my article ‘Do Bicycle Hubs Hang from the Rim?‘ I explain that in order to understand how bicycle wheels work they need to be thought of as a complete structural system, with the hub, rim, and every spoke contributing to the strength and stability of the wheel. In this article I am going to explore how bicycle wheels actually carry a load in more depth, in order to give some theoretical background which can be used to make informed decisions when it comes to choosing components, spoke counts, and lacing patterns for wheel building.
Basic Force Transfer in Bicycle Wheels
As a bicycle wheel turns, a flat spot develops in the rim right above where the tire contacts the ground. This causes the spoke immediately above this point to slacken fairly significantly, and the tension in the remaining spokes to slightly increase. The amount each spoke contributes to the load transfer within the wheel is proportional to how much the tension changes in that particular spoke, which means that at any given moment the most critical spoke is the spoke most immediately above the point where the tire contacts the ground.
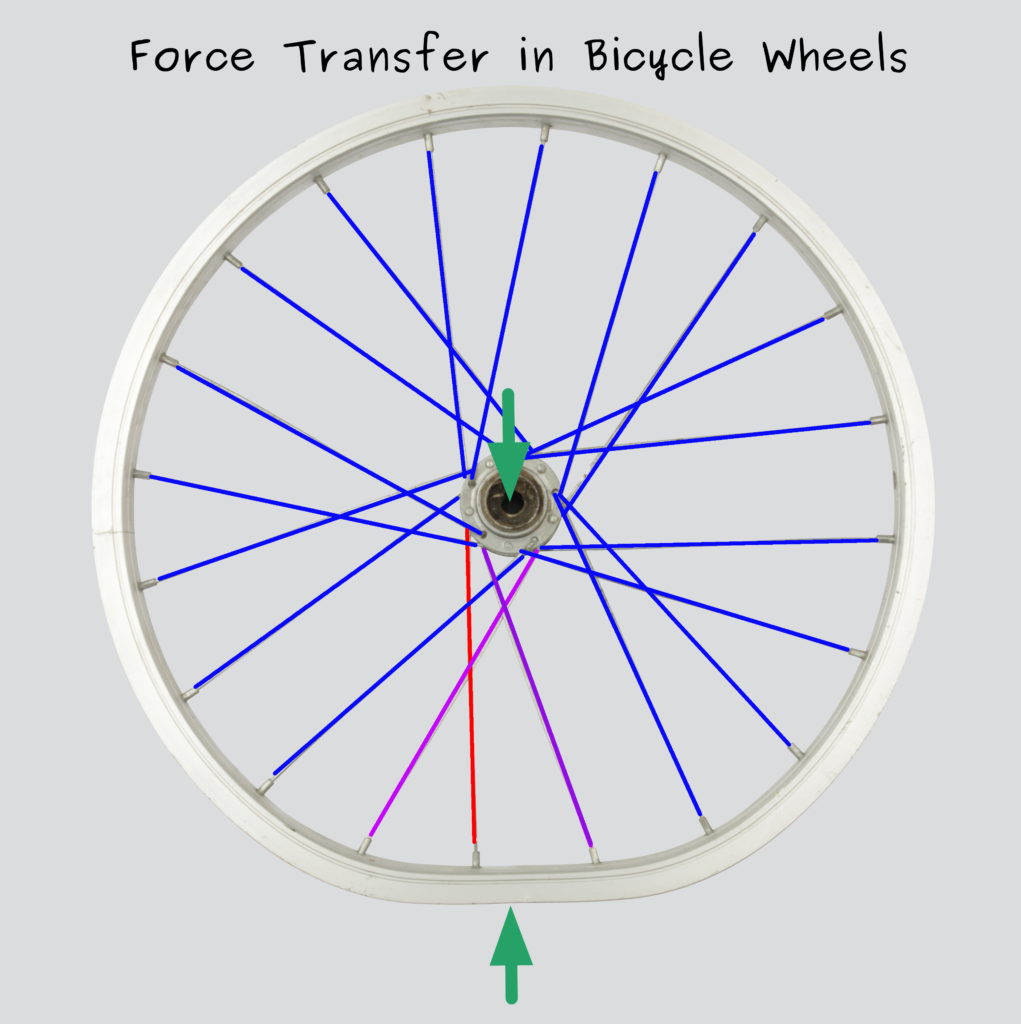
Red = Decrease in Tension
Blue = Increase in Tension
Even though the spoke immediately above where the tire contacts the ground is the most active in transferring the weight of the bike to the ground, cutting that spoke would not cause the wheel to fail catastrophically. Instead, this would cause the forces in the wheel to redistribute, which would throw the wheel out of true, but the actual load which would have been carried by the cut spoke would simply be transferred to other nearby spokes and the wheel would remain largely intact. If this process were continued, each time another spoke was cut cut the wheel would find a new equilibrium, with the rim coming more and more out of true each time but the load largely being carried by the remaining intact spokes until a critical moment where so many spokes have been cut that the rim bends, leading to catastrophic failure. In the real world, the wheel would typically come out of true to the point where it could not turn within the bike frame before this point would be reached.
This understanding of the way the forces transfer through a bicycle wheel immediately leads us to draw several important conclusions:
- The tension in any given spoke only ever increases very slightly, suggesting that the risk of a spoke breaking due to excess tension is low (and in practice this really only occurs if a spoke is over-tensioned during wheel building or truing).
- If the wheel is under-tensioned, it is possible for the spoke above the point of ground contact to slacken completely, especially if the wheel experiences an impact due to i.e. a curb. This is very dangerous because the spoke then experiences a shock as the wheel turns and the spoke returns to its original tension, significantly increasing the risk of a spoke breaking due to fatigue. Fatigue is damage to a spoke which occurs over time as it repeatedly experiences cycles of stretching and relaxing, and it accumulates rapidly if a spoke experiences complete relaxation during use.
- The amount the rim bends is directly proportional to its stiffness. Stiffer rims bend less and therefore cause the spoke above the point of ground contact to slacken less, resulting in a wheel which can carry more weight before the spokes slacken completely. Stiffer rims also cause the load to be shared by more spokes because the force from the ground is ‘spread out’ more along the circumference of the rim. This makes the wheel stronger and also reduces fatigue damage, because the tension in any individual spoke is reduced by less as the wheel turns. In addition, the overall tension in a wheel with a stiffer rim can be lower, because it takes more force to slacken an individual spoke completely if a stiff rim spread the load across more spokes.
- If a wheel has more spokes, the spoke holes will be spaced closer together in the rim. As with a stiffer rim, if the spokes are spaced closer together, more spokes will actively be carrying the weight of the bike, so each spoke will be carrying less of the overall load. This, in turn, makes the wheel stronger, reduces fatigue damage, and allows the wheel to be built with lower overall tension.
Bicycle Wheel Failure Modes
So what actually causes a bicycle wheel to fail, and what determines its strength? More than any other factor, the strength of a wheel in the real world is determined by its ability to prevent the spokes from completely slackening during use, which is extremely damaging because it causes fatigue damage to rapidly accumulate in the spokes, and because it causes a ‘shock’ which can cause an already-damaged spoke to snap. The analysis above suggests that this resistance to slackening can be increased by either increasing spoke tension, increasing the number of spokes, or increasing the stiffness of the rim.
The second most important factor is a wheel’s resistance to spoke fatigue, which is quite closely related to its resistance to a spoke slackening completely. Spoke fatigue depends on how much the stress (which is proportional to tension) changes in each spoke as a wheel turns, and how often this change in stress occurs. Fatigue life increases when spoke count increases because the forces are transferred through more spokes, so the tension in each individual spoke changes less each time the wheel rotates. Spoke fatigue life also increases when rim stiffness increases, because the tension in the spokes changes less as the wheel turns if the rim bends less.
Although all spokes are engineered to be resistant to fatigue, spoke type also has an effect on fatigue. In particular, double butted spokes are cold worked to be thinner in their middle section, which means that they stretch more in this straight region as they are loaded and unloaded. This protects the vulnerable J-bend and nipple ends of the spokes because the stress within the metal is transferred away from the ends of the spokes, increasing fatigue life. This topic will be explored in more detail in a future article about spoke selection.
Now let’s look at some other possible ways in which a bicycle wheel could fail. I have already alluded to the fact that over-tensioning spokes is much less dangerous than under-tensioning, because the tension in the spokes only increases very slightly as the wheel is loaded. We’ll also see later on that even if a spoke actually is over-tensioned, rather than immediately failing it will simply ‘yield’, or relax slightly, because the steel itself used to make spokes has significant ductility built into it. Spokes in use almost always break due to fatigue rather than their ultimate strength being exceeded, however, it certainly is possible to break a spoke during wheel building or truing, especially if a nipple is seized or if the spoke is twisted as it is tensioned.
Another point of failure is the rim, and if the recommended spoke tension is exceeded a spoke could pull through the rim, but if the spoke tension is lower than the maximum allowed by the rim this is unlikely. It is also virtually impossible for the rim to fail due to vertical bending because rims are very strong and stiff in the radial direction. In fact, the spoke above the point of ground contact would slacken completely long before the rim would fail this way, however, a common way for wheels to fail is for the rim to bend outwards, either to the point of complete failure (a ‘tacoed’ rim), or to the point where there is not enough adjustability in the spokes to properly retrue a damaged rim. This does not generally occur during use because rims are engineered to resist the forces encountered during normal cycling, but is a very common failure mode for wheels which are damaged in a collision or car accident.
Like spokes, rims accumulate fatigue damage throughout the life of the wheel, and rims do sometimes fail due to fatigue – however, the fatigue life of rims is generally much higher than that of spokes. This means that spokes will start breaking much before the rim breaks due to fatigue, and a wheel which fails this way can typically relaced with new spokes and the same rim and still have a significant service life. In general, rims are engineered for a certain weight capacity, impact resistance, and fatigue life, and should not fail under normal use as long as the allowed weight is not exceeded.
The last possible point of component failure is, of course, the hub. Hubs, like rims, are generally engineered such that they shouldn’t fail under normal use either. In general, hubs are also simply not particularly significant when it comes to the overall strength and structural performance of a wheel (or particularly sensitive to fatigue) because they don’t really flex the way spokes and rims do as a wheel turns.
The one exception is wheels built with a radial lacing pattern, because in this case the spokes pull perpendicular to the hub flanges. This is the weakest direction because there is the least amount of material between the spoke hole and the edge of the flange, and certain hubs are not rated to allow radial lacing. I don’t agree with radial lacing on principle for a number of strength related reasons, one of which is potential hub failure – but if you are considering lacing a bicycle wheel radially I would highly recommend proceeding with caution and doing some research first.
Torsion
The analysis above explains how a wheel carries the weight of a bicycle, the rider, and any luggage, but wheels have to contend with other forces as well. The most significant of these is torsion due to pedaling and, in modern times, e-bike motors and disc brakes. This torque is transmitted through the wheel from the hub to the rim through ‘pushing’ and ‘pulling’ spokes, which pull on the rim along its circumference to turn the wheel, forward in the case of pedaling and backward in the case of braking with a disc or hub brake.
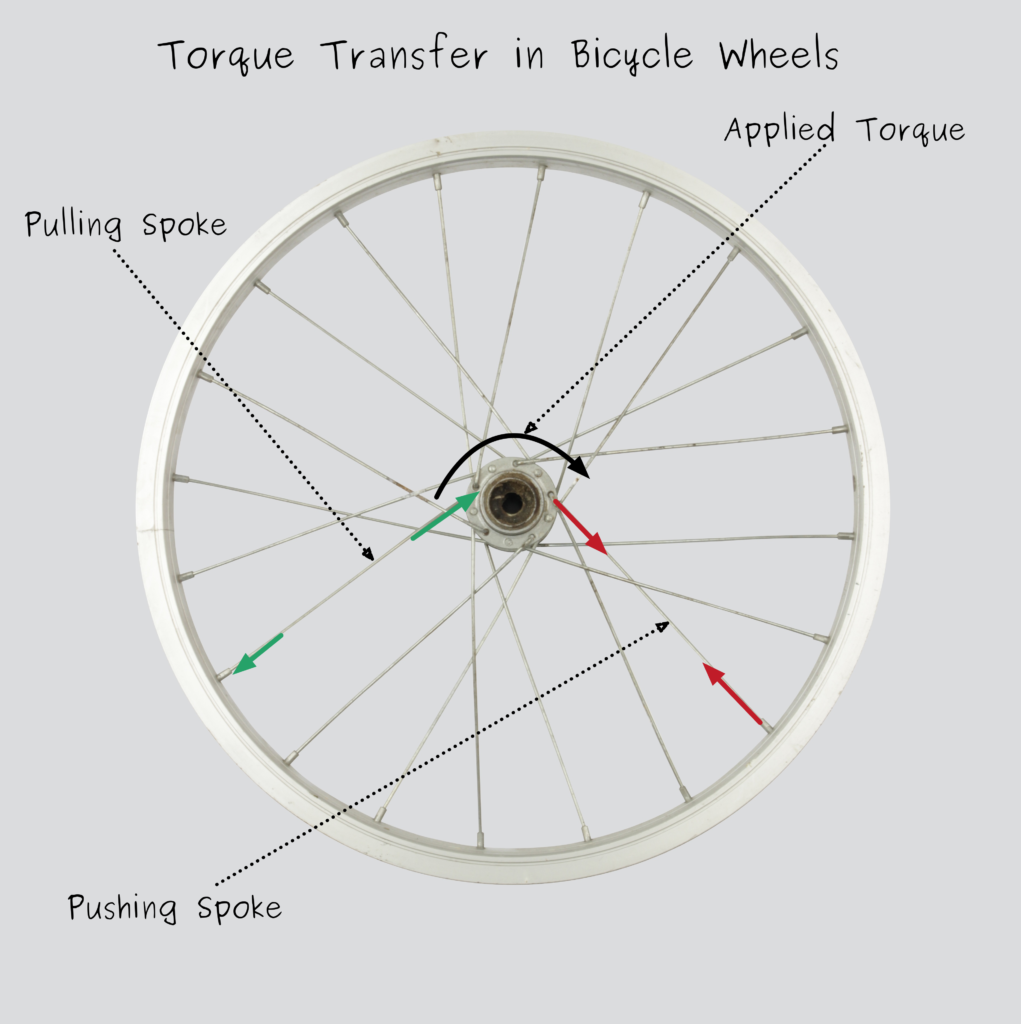
In general, bicycle spokes are very good at transmitting forces straight along their length, either through tension (pulling), or, if a spoke is pre-tensioned, through a reduction in tension, which can also be thought of as a virtual compressive (pushing) force. But because they are so slender, they are not good at transmitting forces through bending. This means that the most efficient way to carry the static weight of the bike is with the spokes laced as straight as possible between the hub and the rim, as it would be with a radial lacing pattern, because this puts the spoke between the hub and the ground exactly in line with gravity.
On the other hand, the most efficient transfer of torque occurs when the spokes exit the hub at a tangent, because this allows the forces caused by a turning hub to transfer straight along the spokes. This also causes the spokes to enter the rim at a slight angle, which is critical because at allows a component of the applied force to pull along the circumference of the rim, turning the wheel. In theory, very little torque transfer is possible in a radially laced wheel because the spokes are perpendicular to the rim, so they can only transfer forces in pure bending. In reality, radially spoked wheels are capable of transfering torque because the hub ‘winds up’, or twists in relation to the rim. This causes the spokes to become slightly angled, allowing torque to be transferred through tension and compression (‘pulling’ and ‘pushing’).
At this point, astute readers will have noted that, in theory at least, there is a conflict between how spokes should be laced to most efficiently transfer radial forces vs. how they should be laced to most efficiently transfer torque. However, there is also the fact that crossing spokes support each other to consider, which means in practice radially laced wheels are actually not the strongest when it comes to resisting radial forces – in fact, the general rule is that more crosses result in a stronger wheel (although a large number of crosses does have other consequences, as I’ll explain in the article about lacing patterns).
The angle of the spokes at the hub varies significantly depending on spoke lacing pattern, but unless the wheel is particularly small or the hub particularly large, the angle of the spokes at the rim is generally fairly close to perpendicular. This, along with the fact that more spoke crosses result in higher strength because crossing spokes support each other, means that the most efficient wheel design overall is generally one in which the spokes exit the hub at as close to a tangent as possible – as long as the angle at the rim is not so extreme that the spoke nipple cannot seat properly.
Although a wheel in which the spokes exit the hub at a tangent is generally the most efficient, a final point to make here is that pedaling, and even braking does not actually change the tension in a bicycle wheel very much – certainly much less than an impact, or even the static weight of a rider does. This means that the way a wheel is designed and laced can actually vary quite a bit from the ‘ideal’ and still be a very strong and efficient structural system, but it is good to keep in mind the general rule that spokes leaving the hub at a tangent result in the most efficient wheel builds.
Asymmetrical Spoke Tension
The last strength topic I would like to address in this article is the issue of asymmetrical spoke tension. If a hub is symmetrical and centered with respect to the rim, as it is in a front rim brake wheel, the spoke tension on the left and right sides of the wheel should be more or less identical. However, if the hub is displaced to the left or right, as it is with any rear hub or with a front hub with a rim or roller brake, the spoke tension ends up being different between the left and right sides of the wheel. The way the hub is centered with respect to the rim is called ‘dishing’.
Dishing affects spoke tension because the closer a hub flange is to the center line of the rim, the closer to vertical the angle of the spokes between the hub and the rim on that side of the bike. Spokes transfer radial forces in proportion to how close to vertical the spoke angle is, which means that the spoke tension increases as the spoke angle becomes closer to vertical. Rear hubs are typically displaced towards the left to accommodate the cassette, which means that they tend to have higher spoke tension on the right side of the wheel, while disc front wheels are displaced to the right, which causes higher spoke tension on the left side of the wheel. The ratio of tension between the left and right sides of a wheel can be significant, for instance the tension ratio of a rear wheel without disc brakes can be close to 2:1, meaning that the tension on the drive side may be nearly twice as high as that on the non drive side.
This is an important concept when it comes to wheel building, because it means that the tension on the drive side of rear wheels (or the disc side of front wheels) must be high enough that the non-drive side can still be adequately tensioned to avoid complete slackening during use. For the purposes of this article, the main thing to realize is that this is why drive-side rear spokes are the most susceptible to breakage. It is sometimes claimed that drive-side rear spokes break more often due to pedaling torque, but this is not correct – it is all about the high tension experienced by these spokes, which means that they are much more active in carrying the weight of the bike, and because they are more active they also absorb much more fatigue damage than the non-drive side spokes do.
Stiffness
Finally, let us briefly explore the topic of wheel stiffness. People who build or purchase bicycle wheels are sometimes interested in having a wheel with a certain stiffness, which they relate to the way the wheel feels in practice. There are two main ways in which stiffness comes into the picture in bicycle wheel design.
The first is radial stiffness, which potentially affects the way a bicycle wheel feels as it rolls across the ground. A stiffer wheel is sometimes seen as ‘harsher’, while a less stiff wheel may be seen as more compliant. In theory, radial stiffness can be affected by the design of the rim, with deeper section rims being more resistant to bending than shallow rims, as well as by the spokes, with more or thicker spokes being more resistant to slackening or lengthening.
The reality is that any bicycle rim is so much stiffer than the spokes that the rim can really not be considered to have a perceptible effect on the stiffness of the wheel. Indeed, although different spoke counts and lacing patterns also have a theoretical effect on radial stiffness, the reality is that none of these factors are of practical significance because of the effect of the tire on the ride quality of the wheel. According to Jobst Brandt’s ‘The Bicycle Wheel’, tires are about one hundred times more elastic than spokes, which are themselves significantly more elastic than rims. This means that any slight variation in stiffness afforded by different spokes or rims is simply ‘swallowed up’ by the compliance afforded by rubber tires.
Compliance is also built into the overall bicycle through flex in frames and forks, handlebars, stems, seatposts, and, in some cases, suspension components. This dilutes the influence of the wheels even further, which means that at the end of the day, effect of changing the components used to build a wheel or changing the way a wheel is laced has essentially zero practical influence on perceived wheel stiffness. Sometimes cyclists will complain that certain wheels are too stiff or not stiff enough, but according to Brandt, this is actually a placebo caused by acoustic vibrations that develop within the wheel at speed.
The second main type of stiffness is lateral stiffness, which is the ability of a wheel to resist the sideways forces that come about mainly through cornering. This stiffness is primarily determined by the lateral ‘bracing angle’ of the spokes between the rim and the hub, with larger angles allowing the spokes to better resist any sideways forces applied to the rim. Spoke bracing angle is determined by hub spacing, with larger spacing resulting in greater bracing angles, and wheel diameter, where smaller wheels have greater bracing angles. A real-world example of where this comes into play is the adoption of boost spacing on mountain bikes, with greater lateral stiffness being one of the primary benefits of larger hub spacing, which is especially important for modern large wheel diameters, particularly 29ers.
The spoke bracing angle is also higher on one side than the other side of asymmetrical wheels, but this phenomenon is a necessary compromise in the design of chain-driven or hub brake bicycles. Spoke count, spoke gauge, and rim stiffness also have a minor affect on lateral wheel stiffness, but these effects are overshadowed by the effect of bracing angle and are therefore do not generally have a significant affect on real-world bicycle wheel stiffness. In general, lateral wheel stiffness is mainly determined by the design of the frame, and bracing angle is not something that can be significantly changed by a wheel builder.
The discussion of radial and lateral stiffness is interesting and good to have a general awareness of, but neither should be seen as important design considerations when building a bicycle wheel. This is because stiffness is proportional to strength, so the primary consideration should actually be strength itself – if a bicycle wheel is strong enough for a given application, it can be assumed to be stiff enough as well.
Along with radial and lateral stiffness, the performance of a bicycle wheel is also affected by its torsional stiffness. This is essentially how much the hub rotates with respect to the rim when a torque is applied, either through pedaling or through braking, and it is sometimes referred to as hub ‘wind-up’. Torsional stiffness is a very minor consideration with crossed lacing patterns, because the crossing spokes, as well as the resulting angle between hub and rim, essentially locks the hub and rim together, nearly eliminating wind-up under real-world pedaling and braking regardless of spoke count or thickness. Wind-up is a significant consideration when it comes to radially laced wheels, however, because the spokes connect perpendicularly between the hub and rim, which means that they need to bend a little in order to allow the wheel to transfer torque. Radially laced rear wheels are capable of transferring torque, because hub wind-up changes the angle of the spokes away from perpendicular and allows the spokes to push and pull along the circumference of the rim, but radial lacing is still not a particularly strong design, and is not recommended, especially for rear wheels or disc-brake front wheels.
Conclusion
Bicycle wheels are complex, and the fact that the spokes are pre-tensioned causes the wheel to behave in ways that are sometimes counter-intuitive. The most critical spokes aren’t the spokes above the hub but rather those between the hub and the ground; however, all spokes are active in carrying the weight of the bicycle. If any one spoke is cut, the equilibrium of the wheel changes, resulting in a decrease in strength and in the wheel coming out of true; with that being said, there is significant redundancy built into the structure of a bicycle wheel, so many spokes could be cut before the rim would catastrophically fail.
In the real world, it is uncommon for spokes to break due to excess tension unless the spokes are twisted or over tightened during wheel building, because as a wheel is loaded the primary effect is that the spoke between the hub and the ground starts to slacken. Instead, spokes tend to fail due to fatigue, which is damage that accumulates as the spokes continually stretch and relax throughout the life of the wheel. Fatigue damage is minimized by using more spokes, a stiffer rim, or specially designed spokes such as double butted spokes to transfer stress increases away from the ends of the spokes. Most importantly of all, it is essential to maintain enough spoke tension so that the spokes don’t slacken completely during normal use of the wheel. It is also possible for spokes to fail due to failure of the rim, but this normally only happens during a collision or impact, which can also cause the rim itself to permanently bend sideways.
Along with the static weight of the bicycle, wheels also have to contend with the dynamic forces imposed as the rider pedals. The most significant of these is torsion, which causes the hub to ‘wind-up’ with respect to the rim. Torsion is most efficiently transferred when the spokes are laced such that they enter the hub at a tangent, and hub wind-up is virtually eliminated in any wheel laced with a cross pattern. Radially laced wheels are very poor at transferring torsion because spokes are very weak in bending, but radially laced wheels wind-up significantly, angling the spokes and allowing torque to be transferred as pushing and pulling along the length of the spokes, the way it is in a cross laced wheel. In general, radial lacing patterns are weak and not recommended, but they are sometimes used for extreme weight savings or for aesthetic reasons.
All rear wheels and disc/hub brake front wheels are ‘dished’ to center the rim over the full width of the hub, rather than between the hub flanges. This causes the lateral ‘bracing angle’ of the spokes to vary between the left and right sides of the wheel, which causes an imbalance in tension between the left and right side spokes. The primary consequence of this is that asymmetrical wheels need to have enough tension to prevent the spokes from slackening completely on the side with lower spoke tension. Asymmetrical wheels, especially non-disc-brake rear wheels, are more susceptible to spoke breakage because the amount of force each spoke carries is proportional to its tension, and the tension in the drive side spokes of rear wheels can be close to twice as high as that on the non-drive side.
A final theoretical consideration in the design of bicycle wheels is stiffness. Sometimes riders will claim that their wheels are either not stiff enough or too stiff, leading to undesirable ride characteristics, but the reality is that the effects of spoke count, type, and rim design on stiffness are minimal. This is because their effects are ‘swallowed up’ by the high elasticity of the tires, as well as the compliance built into the design of the overall bicycle. The one exception is the effect of bracing angle on lateral stiffness, which is primarily a concern for mountain bikes, but this bracing angle is determined by hub spacing which is an inherent parameter built into the design of a specific frameset. For wheelbuilding purposes, the rule of thumb is that if a wheel is strong enough for a given purpose, it is also stiff enough.
In conclusion, although the design of bicycle wheels is complex and their behavior counter-intuitive, their structure is highly efficient overall with a significant amount of built-in redundancy. There are some parameters which can be varied to change the performance of a specific wheel, such as rim type, spoke type, spoke count, and lacing pattern, but the behavior of a wheel is mostly determined by its inherent structure and the engineering done on the spokes and rims. In the next series of articles, I will explore the specific principles of wheel building in detail, and explain how general rules of thumb can be used to create a bicycle wheel that is best suited for a given purpose.
References
- https://www.quora.com/When-riding-a-bicycle-are-you-suspended-from-the-rim-by-the-spokes-between-the-hub-rim-at-the-tallest-point-of-the-wheel-or-are-you-supported-by-the-spokes-between-the-hub-the-rim-pushing-against-the-rim-tyre-at-the-lowest-point
- http://hea-www.harvard.edu/~fine/opinions/bikewheel.html
- https://www.astounding.org.uk/ian/wheel/index.html
- Burgoyne, C. J., and R. Dilmaghanian. “Bicycle wheel as prestressed structure.” Journal of Engineering Mechanics 119.3 (1993): 439-455.
- Papadopoulos, Jim M. “Bicycle wheel as prestressed structure.” Journal of Engineering Mechanics 121.7 (1995): 847-849.
- Brandt, Jobst. The Bicycle Wheel. 3rd ed., Palo Alto, California, Avocet, 1993.
- Pippard, AJ Sutton, and W. E. Francis. “XX. On a theoretical and experimental investigation of the stresses in a radially spoked wire wheel under loads applied to the rim.” The London, Edinburgh, and Dublin Philosophical Magazine and Journal of Science 11.69 (1931): 233-285.
- Ford, Matthew. Reinventing the wheel: Stress analysis, stability, and optimization of the bicycle wheel. Diss. Northwestern University, 2018.
- https://www.sheldonbrown.com/wheelbuild.html
- https://www.sheldonbrown.com/special-spoking.html
- https://spokecalc.io/spoke-tension-the-difinitive-guide.php#:~:text=On%20average%2C%20tension%20in%20right,only%20be%20tensioned%20at%2070kgF.